Nuts Industry Trends for 2024
There is a long list of nuts that may be conveyed in your facility. Almonds, brazil nuts, cashews, hazelnuts, macadamia, peanuts, pecans, pine nuts, pistachios, and walnuts are a few common types of nuts that are consumed globally. The United States Nuts Market is projected to grow at an annual rate of 5% for the next five years. This growth trend mirrors what has happened in the past 10 years. Here is an example of the growth rate of roasted nut and peanut butter manufacturing in the past 10 years.
What is unique about conveying nuts?
Nuts are brittle and sensitive to motion and free fall, a common occurrence with certain types of conveying. Nut production and processing facilities either handle a single type of nut or a variety of nuts for various purposes. Nuts can be processed for their oils, for nut butter, or for packaging and sale as whole nuts or as ingredients in a wide range of food products. Selecting the best conveyor system for the nuts you are conveying is critical.
Finding #1: Are you ready for the upcoming growth in the nut industry?
87% of facilities processing nuts are increasing their budget for conveying equipment and maintenance in the next 12 months. 34% tell us that they are significantly increasing the budget needed to meet growth opportunities. Growth in the industry is projected to continue in the next 5+ years, so advanced planning to meet that growth is critical to your future success. Why the increase in the budget? The increase is in response to how much these businesses grew in the past year. An astounding 71% of facilities experienced 11% or more growth in the past year. With this type of growth, facilities must plan to accommodate the increased conveying capacity of nuts to meet the growing demand.
Finding #2: Professionals frequently evaluate their conveying systems.
How frequently do professionals in the nut industry evaluate their systems? We can safely say that the answer is “sooner rather than later!” 96% of the professionals surveyed evaluate their systems at least every 6 months and 39% do it monthly.
Finding #3: Energy efficiency is a BIG deal.
What contributes to energy efficiency? The size of the motor and the amount of horsepower required to run a conveying system can have a major impact on production costs. What conveying system is the most energy efficient for conveying nuts? Cable and disc conveyors are #1 by a wide margin, at 54%
Here are two questions to ask regarding energy and efficiency:
- How much energy will this system use?
- Is there a high or a low cut-off point at which this system becomes inefficient?
Finding #4: What type of conveying system optimizes a facility’s workspace?
An important consideration of growth is your workspace and facility requirements. What conveying systems are best for the space that you have available? Are you optimizing the space you have available?
94% of nut industry professionals told us that they are optimizing their workspaces and facility requirements. How are they doing it? According to the nut processing experts surveyed, the #1 conveying system (50%) for maximizing available space is cable and disk conveyors. Bucket elevators (43%) and pneumatic conveyors (43%) were a distant second place in optimizing a facility’s workspace.
The fact is, you cannot have a conveyor system without taking up some floor space. And depending on the size and layout of your facility, the amount of space you have to work with will be different.
When planning the layout of your facility, it is important to take into account all the specifics. Do you need multi-directional conveying? Multi-floor conveying? Do you have a lot of horizontal space or vertical space? Or both? What about any sharp turns or corners, or potential existing equipment or barriers?
Your answers to these questions will help you determine the best conveyor type for your needs. It could be an overhead conveyor, a vertical conveyor, one that transports material at an angle, or similar. For example, if you need to move roasted or raw material between floors at a steep angle, a belt conveyor would not be the best option.
A modular conveyor, such as a Cablevey tubular drag conveyor, is perfect for facilities both with ample and limited space. These conveyors can be configured to fit almost any layout, and they can be modified in time as your facility grows or changes.
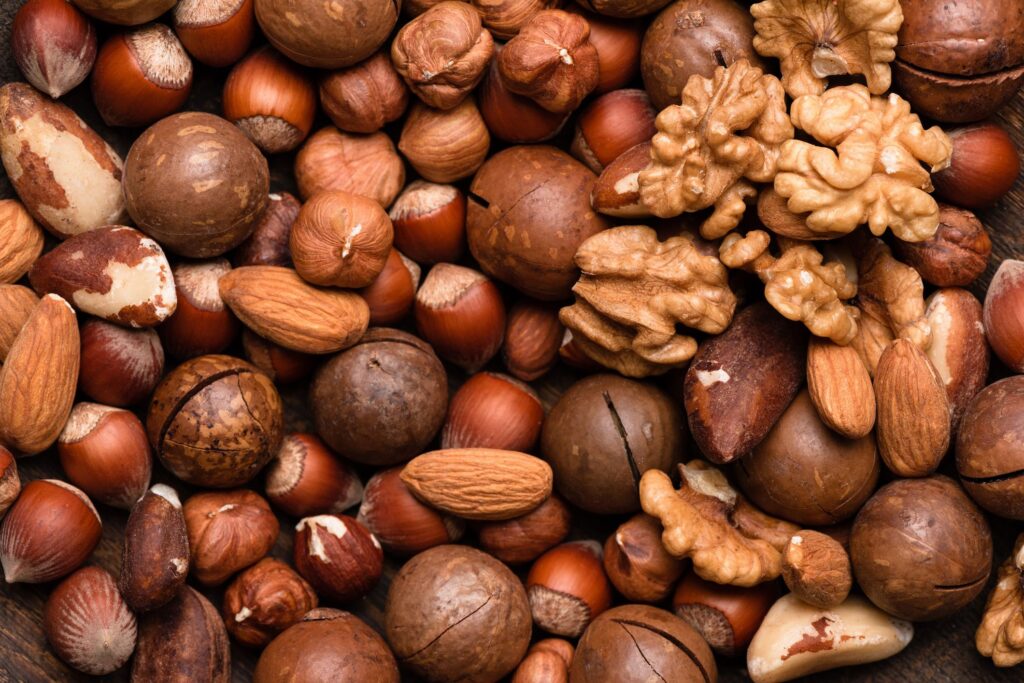